Understanding Centrifugal Screens: Essential Solutions for Efficient Filtration
In industrial and processing applications, the need for precise, high-performance filtration is critical to ensure product quality, efficiency, and safety. One of the most effective and widely used filtration technologies is the centrifugal screen. These systems are pivotal in industries ranging from food processing to pharmaceuticals, chemical production, and oil & gas. In this article, we’ll explore the benefits, functions, and applications of centrifugal screens, as well as why they are indispensable in many industries.
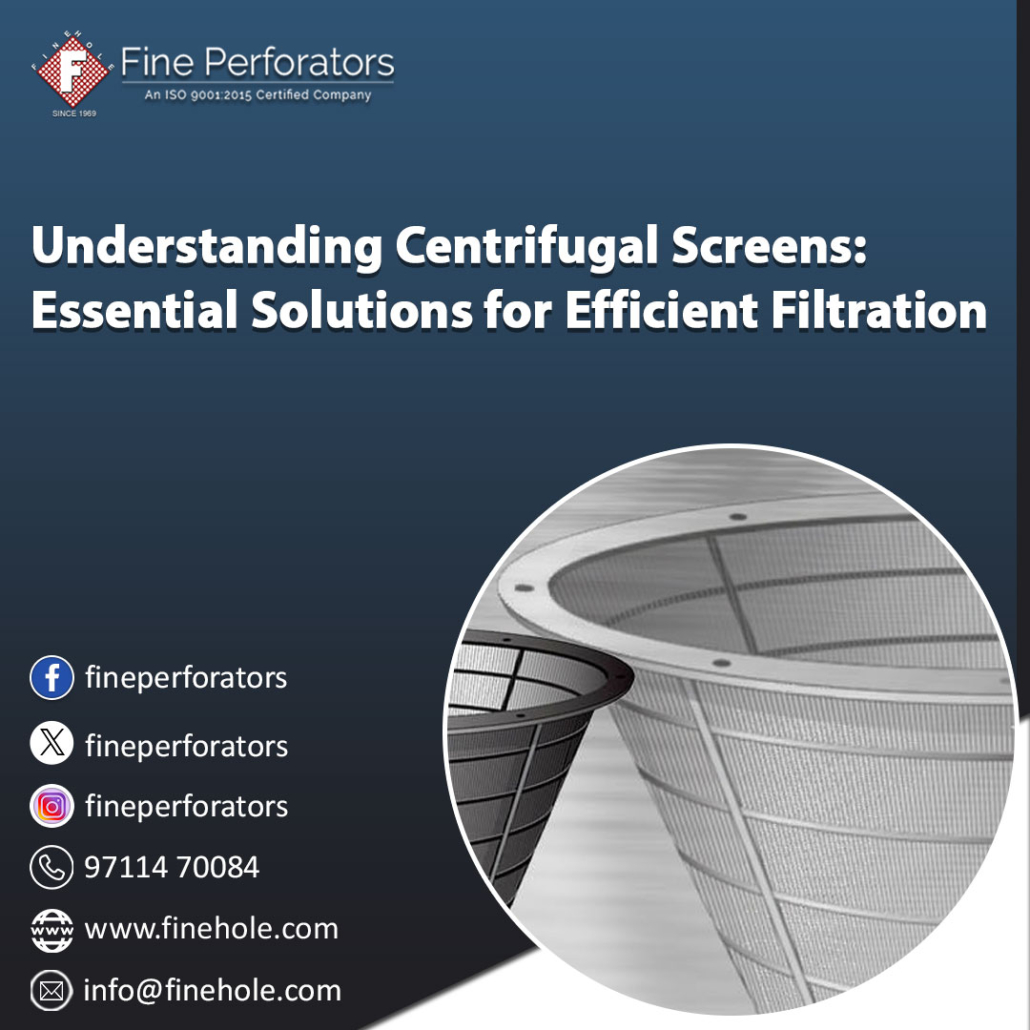
What is a Centrifugal Screen?
A centrifugal screen is a type of filtration device designed to separate solids from liquids or gases using centrifugal force. This process takes advantage of the principle that heavier particles, when subjected to high-speed rotation, are pushed outward to the edges of the screen, while lighter components are carried towards the center. The centrifugal action effectively separates fine particles from liquids or gases, leaving behind cleaner material.
This technology is commonly used in situations where traditional filtration methods—such as gravity filtration or pressure filters—might not be efficient enough to remove extremely fine particles or operate under demanding conditions.
How Do Centrifugal Screens Work?
The working mechanism of a centrifugal screen is based on centrifugal force. In a typical centrifugal screen, the material (liquid or gas mixed with solids) is introduced into a rotating drum or basket. Due to the drum spinning at a high speed, centrifugal force is generated and as the material is subjected to this force:
- Heavier particles (the solids) are pushed outward, towards the walls of the screen, where they are trapped by a fine mesh or perforated surface.
- Lighter particles and the fluid or gas pass through the mesh or perforated screen and are expelled from the system, leaving behind a cleaner, purified substance.
This technology is incredibly efficient because it accelerates the filtration process, especially when dealing with fine particles that other filtration systems may miss.
Key Benefits of Centrifugal Screens
Centrifugal screens offer several distinct advantages over other filtration methods:
- High Efficiency
Centrifugal screens are designed for high-efficiency filtration, meaning they can handle large volumes of material while effectively separating fine particles. This makes them ideal for industries where high throughput is crucial, such as in food and beverage production, or for large-scale chemical processes.
- Enhanced Precision
Centrifugal force can precisely separate particles based on their size and density, resulting in cleaner products. The high-speed rotation allows for the filtration of even the finest particles that may otherwise slip through traditional methods.
- Reduced Maintenance
Since centrifugal screens do not rely on pressure or gravity to separate particles, they generally experience less wear and tear than other filtration systems.
- Energy Efficiency
Despite their high performance, centrifugal screens can be highly energy-efficient, especially when designed to operate at lower speeds while still maintaining effectiveness. This makes them a cost-effective option for industries looking to reduce energy consumption.
- Versatility
Centrifugal screens are highly versatile and can be used in a wide range of applications across multiple industries, handling various materials, from food products to chemicals and pharmaceuticals. Their adaptability makes them an essential tool in industries where purity and precision are paramount.
Applications of Centrifugal Screens
Centrifugal screens are widely used across a broad spectrum of industries. Here are some common applications:
- Food and Beverage Industry
In food processing, centrifugal screens are used to separate solid particles from liquids, ensuring that beverages, oils, syrups, and other consumables are free from unwanted debris. For example, in juice production, centrifugal screens help to remove pulp, seeds, and other solid materials, leaving behind a smooth, clear product.
- Pharmaceutical Manufacturing
Centrifugal screens play a crucial role in pharmaceutical manufacturing, particularly in the production of fine powders, active ingredients, and other raw materials. In these settings, cleanliness and purity are paramount, and centrifugal filtration systems can efficiently remove contaminants from powders and liquids, ensuring compliance with strict industry standards.
- Chemical and Petrochemical Industries
In the chemical industry, centrifugal screens are employed to filter solids from liquids or gases in chemical processes. They help maintain the purity of chemical products and ensure that processes run smoothly by removing particles that could interfere with production. Similarly, in oil and gas extraction, centrifugal screens separate impurities from crude oil and natural gas, helping to refine these resources.
- Wastewater Treatment
Centrifugal screens are used in wastewater treatment plants to filter out solids and other contaminants from wastewater. By efficiently separating solids from water, they help to reduce the load on downstream treatment processes, improving overall efficiency and ensuring that treated water meets environmental standards.
- Mining and Mineral Processing
In the mining industry, centrifugal screens are used to separate fine particles from slurry and other mixtures. This is crucial in mineral processing, where it is important to separate valuable minerals from waste material in an efficient and cost-effective manner.
Choosing the Right Centrifugal Screen:
When selecting a centrifugal screen for a specific application, several factors should be considered:
- Particle Size and Material Type: Different industries and processes require different mesh sizes and configurations. Fine perforations are required for smaller particles, while larger perforations are suitable for coarser materials.
- Speed and Efficiency: The speed at which the centrifugal screen operates will impact its efficiency. Higher speeds can improve filtration but may consume more energy. Finding the balance is key to optimizing performance.
- Capacity: Depending on the volume of material being processed, selecting a centrifugal screen that can handle the required throughput is essential.
- Material Durability: The material from which the screen is made must be compatible with the substances being filtered. For example, a stainless steel screen is ideal for corrosive liquids, while other materials might be better for less aggressive substances.
Conclusion
Centrifugal screens are indispensable filtration tools that bring high efficiency, precision, and reliability to a wide range of industries. From food processing to chemical manufacturing, their ability to separate fine particles from liquids and gases makes them a valuable asset in maintaining product quality and ensuring operational efficiency. As industries continue to evolve and demand more advanced filtration solutions, centrifugal screens will remain a cornerstone of effective filtration technology.
Whether for large-scale industrial use or specialized processes, centrifugal screens offer the efficiency, versatility, and long-term durability that businesses need to thrive in today’s competitive environment. Fine Perforators are the premier manufacturers and exporters of Centrifugal Screens in India, contact us today to kick start your journey with our premium Screens!
Source: https://fineholeindia.nethouse.ru/articles/understanding-centrifugal-screens-essential-solutions
Leave a Reply
Want to join the discussion?Feel free to contribute!